Разработаем композитное изделие под «ключ». Изготовление матриц, подбор компонентов, отработка технологии и выпуск опытных партий изделий.
Метод вакуумной инфузии может использоваться для создания прочных и легких композитных материалов. Такие материалы применяются в авиации, автомобильной промышленности, ветроэнергетике и других областях. Вакуумная инфузия в настоящее время является наиболее перспективной технологией получения композитов. Этот метод, в сравнении с другими, обладает рядом преимуществ:
- Получение композита с высоким содержанием армирующего материала.
- Низкая пористость изготавливаемых изделий из композитов;
- Отсутствие полуфабрикатов с малым сроком жизни (препрегов, волокнитов), время подготовки и сборки вакуумного мешка неограниченно;
- Отсутствие необходимости использовать в технологическом процессе дорогостоящих автоклавах, прессов и инжекционных систем;
- Возможность изготовления больших деталей целиком без разделения на составные части.
Процесс вакуумной инфузии заключается в заполнении жидким связующим пор в предварительно отвакуумированном пакете (Рис 1) из армирующего материала (стопки угле-стеклотканей) уложенным в специальной оснастке — матрице или форме.
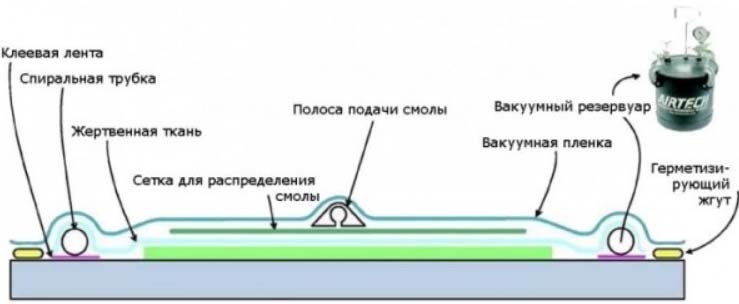
Матрицы, в которых осуществляется вакуумное формование изделий из композитов изготавливаются из различных материалов, наиболее часто используются стеклопластиковые (для опытных или малых серий изделий) и металлические матрицы (для серийного выпуска изделий).
Процесс производства металлических матриц аналогичен процессу изготовлению пресс-форм для литья на ТПА, описанный в предыдущем разделе. При изготовлении стеклопластиковых матриц возможны два варианта решения этой задачи.
Первый вариант — непосредственное использование изделия, которое необходимо скопировать в виде мелкосерийной партии деталей. Для этого на поверхность детали наносится антиадгезионный состав (восковая смазка). Затем слой гелькоута, после отверждения гелькоута накладываются несколько слоев стеклоткани, пропитанной эпоксидными или полиэфирными или полиурета — новыми связующими. И завершает процесс приклеивание к этому «сэндвичу» нескольких слоев тканного полотна из стеклоровинга и формирования из него ребер жесткости. Далее изъятие исходной детали из формы и нанесение на поверхность полученной таким образом матрицы нескольких слоев восковой смазки.
Второй вариант предполагает разработку 3-D модели изделия или детали, передачу этого файла на станок с ЧПУ и изготовление на нём первичного позитивного пуансона («болвана») из плиты МДФ или фанеры. «Болван» может использоваться или в виде одноразовой формы для вакуумной инфузии опытной детали или для изготовления стеклопластиковой формы аналогично описанному выше процессу.
Наша компания предлагает свои навыки в изготовлении стеклопластиковых и металлических матриц:
- можем изготовить «болван» из МДФ без финишной обработки на ЧПУ, самый быстрый и недорогой вариант.
- «болван» из МДФ с полимерным слоем, финишно обработанным на ЧПУ.
- стеклопластиковую матрицу, снятую с изготовленного нами «болвана». Следует учитывать, что «болван» из МДФ чаще всего является одноразовым изделием ввиду низкой прочности его материала, поэтому рекомендуем заказывать этот третий вариант.
- можем изготовить металлическую матрицу (алюминиевую) по вашей 3-D модели или по предоставленному вами изделию на нашем ЧПУ-станке.
Примеры изготовленных «болванов» и матриц.
Пример разработки и изготовления оснастки для производства изделий из полимерных композиционных материалов представлен на примере крюка хоккейной клюшки.
На первом этапе производится обработка модели будущего изделия и проектирование оснастки в соответствии с выбранной технологией производства (рис. 2, 3).
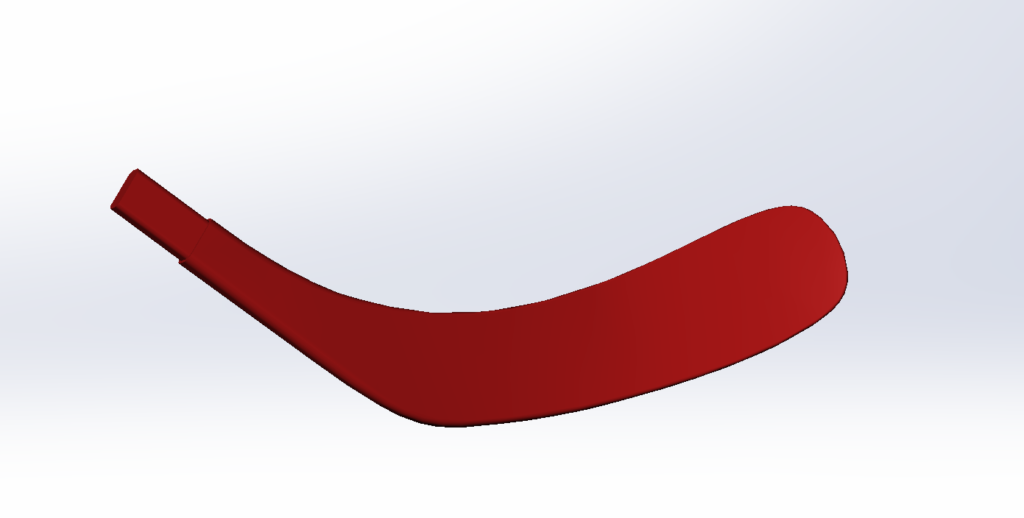
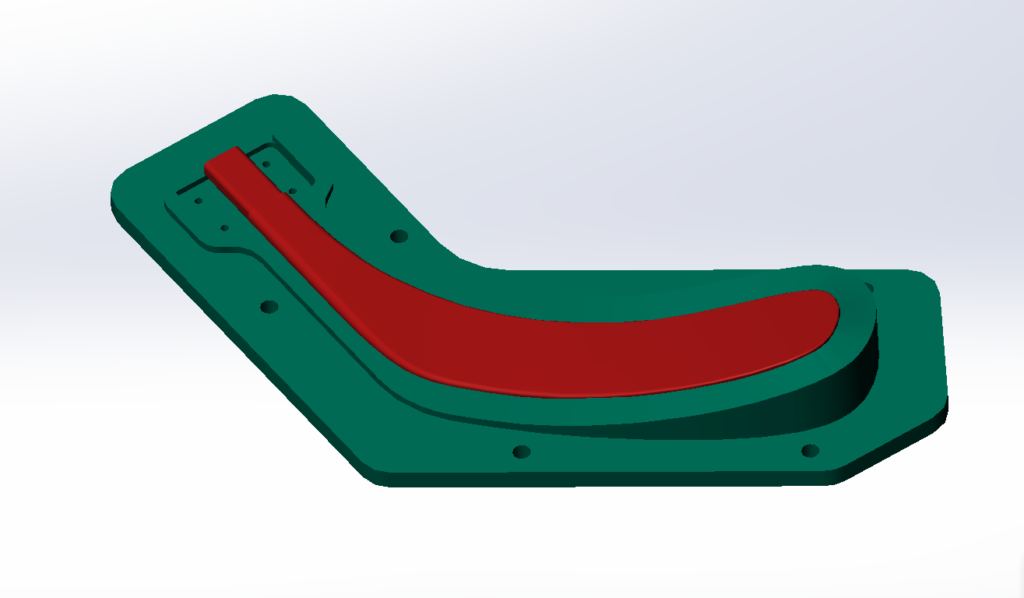
Для изготовления композитной пресс-формы необходимо создать мастер модель из МДФ, с которой в дальнейшем будет сниматься будущая пресс-форма (рис. 3).

По завершении чистовой обработки модель пропитывается эпоксидным связующим для создания прочного верхнего глянцевого слоя (рис. 4). Затем повторно запускается чистовая обработка пропитанной заготовки. Внешней вид изготовленной мастер-модели после всех подготовительных операций представлен на рис. 5.
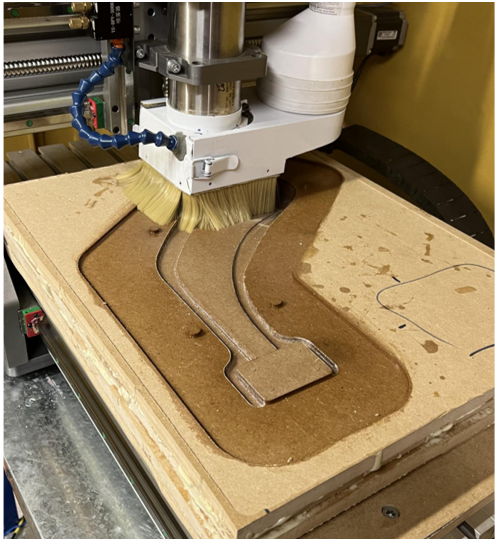
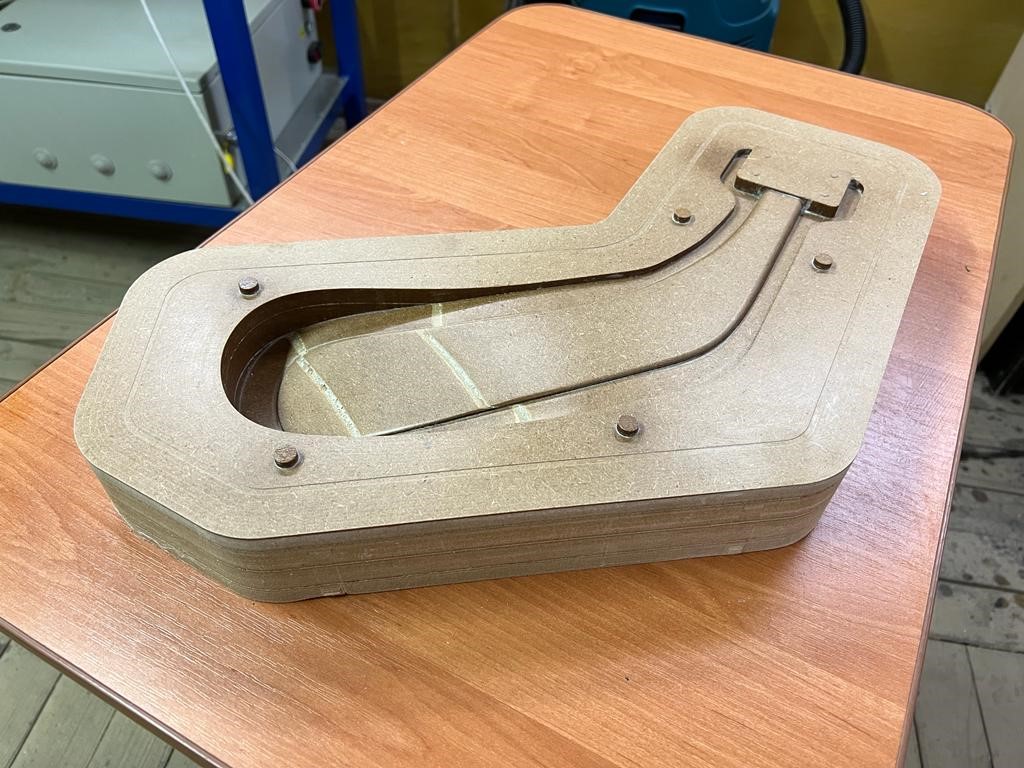
Далее готовая мастер модель покрывается описанными ранее разделительными составами и гелькоутом. После укладки всех необходимых слоев армирующего материала, пропитки их эпосидным/полиэфирным связующим и дальнейшего отверждения (постотверждения) композитную оснастку можно считать готовой для дальнейшего использования.
На рис. 6, 7 представлены модель и пример изготовленного углепластикового рефлектора для отработки технологии производства изделий на основе полиуретановых связующих методом ваккумной инфузии.



Сроки изготовления зависят от габаритов, сложности, количества слоев, загруженности производства.
Ориентир: разработка и изготовление трехслойной матрицы средней сложности габаритами 600x600x200мм занимает около 10-15 дней.
При изготовлении «болвана» работаем преимущественно с МДФ с нанесенным полимерным слоем. Так же стремимся к снижению количества ручного труда. Наши «болваны» из МДФ с нанесенным полимерным слоем, обработанным на ЧПУ станке, пригодны для дальнейшей работы с ними почти без необходимости ручной шлифовки.
При рабочей высоте изделия до 60мм работа выполняется за 1 этап. С большей высоте изделие разбивается по вертикали на слои и изготавливается с поэтапным наращиванием слоев. На выходе имеем цельное изделие требуемой высоты.
Наши возможности
Максимальные габариты цельного изделия/части изделия:
— XY (горизонтальные габариты): 440 х 640 м ;Z (высота): 120 мм.
О точности изготовления
Наше оборудование позволяет изготавливать изделия с точностью порядка 0.1 мм/0.6 м по горизонтальным габаритам и с точностью до 0.1 мм/120 мм по высоте.
Следует учитывать, что обычно первичные изделия («болваны») изготавливаются из пластиковых модельных плит или МДФ с полимерным покрытием. Эти материалы склонны к большим колебаниям линейных размеров при изменении температуры и влажности, чем металлы. Предельная точность этих материалов не превышает 0.5мм/1м при изменении температуры на 20 градусов.
Таким образом мы считаем, что точность изготовления ограничена материалом. В подавляющем большинстве случаев этой точности достаточно.
Что требуется для заказа
Для начала работы предпочтительно иметь 3D-модель изделия. Ограничиться можно чертежами, эскизами, фотографиями, набросками или натуральным изделием.
Перед непосредственным запуском производства матрицы для согласования с заказчиком можем предоставить чертеж с размерами.
Процесс работы предполагает следующие этапы:
изучение технического задания — проектирование — согласование— изготовление «болвана» — изготовление матрицы.
Из чего складывается стоимость
Стоимость определяется индивидуально, в зависимости от геометрических характеристик изделия и расхода сырья. В большей мере на цену влияет машинное время, затраченное на производство.
Доставка осуществляется транспортными компаниями из г. Москва в любой город РФ за счет заказчика.
Для оценки заказа просим обращаться в раздел КОНТАКТЫ.